Dans les petits entrepôts, la combinaison de plusieurs systèmes de stockage est rare. En revanche, plus ils sont grands et plus la marchandise à stocker est variée, plus la combinaison de systèmes différents est fréquente.
L’article traitant des « différences de capacité entre les systèmes » présente des cas combinant des rayonnages conventionnels et par accumulation, ainsi que des critères à prendre en compte pour choisir le bon système.
Cependant, les systèmes de stockages pour les entrepôts de moyenne et grande taille ne se limitent pas uniquement aux rayonnages compacts et conventionnels, il est commun de les associer avec des systèmes spécialement conçus pour le picking, et également de combiner différentes solutions de stockage pour picking.
De fait, l’association de systèmes de stockage pour bacs ou produits en vrac répondant conjointement aux principes de « produits vers l’homme » et de « l’homme vers le produit » est de plus en plus fréquente. Chaque système offre un fonctionnement optimal de l’installation, le tout est de savoir comment bien associer les différentes solutions de stockage.
La recherche de la solution optimale a pour objectif de gérer individuellement les produits pour ensuite, les regrouper en fonction de leur rotation (A, B et C), de leur famille, de leur taille et de la méthode de préparation de commandes appliquée.
Toutes ces données sont accessibles par l’analyse de la base de données des articles. Il est donc possible de déterminer, par exemple, s’il convient d’établir des zones de stockage et des modes opératoires différents, auquel cas, il sera nécessaire d’anticiper l’aménagement d’une zone de consolidation des commandes.
Plusieurs exemples d’associations de systèmes sont présentés ci-dessous, et donnent une idée des diverses configurations possibles (quasiment illimitées) :
Exemple 1. Le picking unitaire |
|
Dans cette configuration, quatre zones sont définies et les opérations sont gérées par un WMS. Les produits de grande consommation sont stockés sur des rayonnages dynamiques pour picking équipés de dispositifs pick-to-light (1). Les produits de moyenne consommation sont stockés au niveau des carrousels horizontaux (2), et les produits de basse consommation sont situés au niveau des rayonnages conventionnels installés sur une plateforme (3). Enfin, la zone de consolidation (4) est réservée pour le regroupement des commandes préparées dans les autres zones de l’entrepôt. Les différentes zones de préparation de commandes communiquent avec la zone de consolidation grâce à un circuit de convoyeurs automatiques pour bacs. Avec cette configuration, l’espace disponible sous la plateforme (également équipée d’un élévateur pour relier la zone des rayonnages conventionnels au convoyeur) peut servir au stockage des commandes prêtes à être expédiées. |
Exemple 2. Le picking unitaire presque entièrement automatisé |
|
Ce type d’installation se développe car elle réduit les coûts d’exploitation. C’est une solution entièrement intégrée. Chaque zone est aménagée avec un système de stockage, de picking et de manutention adapté aux caractéristiques du type de produit stocké en vue d’optimiser chaque opération de l’installation. Un système de transport des marchandises interne, entièrement automatisé a été installé afin de relier les différentes zones entre elles et éviter l’intervention humaine ou l’utilisation d’engins de manutention. Grâce à ce système, les commandes sont automatiquement triées par destination et itinéraire. Dans les installations d’une telle complexité, il est indispensable de disposer d’un système de gestion d’entrepôt (WMS) adapté, chargé de contrôler l’ensemble des opérations. |
Exemple 3. Rayonnages à palettes combinés à un magasin automatique pour bacs miniload |
Avec ce type de configuration, le magasin automatique Miniload est situé à l’intérieur d’un entrepôt équipé de rayonnages à palettes pour le stockage de produits de moyenne et grande dimension, et d’articles à consommation variable. Quatre zones de picking différentes ont été aménagées :
L’ensemble du système fonctionne de manière intégrée, comme une unité de travail. Lorsque la préparation de commandes par vague commence, la première tâche pour les opérateurs est de préparer des bacs complets et les placer sur les convoyeurs pour qu’ils soient automatiquement transférés vers la zone de consolidation. Une fois cette phase terminée, les opérateurs placent les articles en vrac, de moyenne et haute consommation, dans les bacs. Les commandes terminées suite à cette étape sont directement envoyées vers la zone de consolidation ; les autres sont transférées vers l’avant du magasin automatique Miniload afin qu’un opérateur finalise la commande et l’envoie vers la zone de consolidation. Les autres de zones de l’entrepôt sont indépendantes et les commandes sont directement consolidées sur les quais de chargement. De plus, le système de gestion d’entrepôt est capable de décomposer et de gérer toutes les commandes et toutes les zones de l’entrepôt. |
Exemple 4. Solution pour entrepôt frigorifique, à température négative |
Cette configuration d’entrepôt est équipée de rayonnages à palettes dynamiques pour des produits de grande consommation à rotation élevée. Des rayonnages à palettes sur bases mobiles, Movirack, ont également été installés pour les produits à rotation B et C (le niveau inférieur est lui destiné au picking sur bacs individuels). L’entrepôt a également été aménagé avec des rayonnages conventionnels pour le stockage de produits B et C, cependant, contrairement aux précédents, ils sont statiques pour optimiser l’espace disponible, notamment les espaces irréguliers. L’ensemble de ses zones sont desservies par un circuit de convoyeurs qui transportent automatiquement la marchandise, et sert également de buffer pour les commandes préparées ; et c’est la raison pour laquelle un ensemble de convoyeurs a été installé près des quais. La préparation de commandes est effectuée à l’aide d’appareils de radiofréquence ou d’un système de préparation vocale, aussi appelé voice picking. La seconde option est idéale et surtout adaptée aux conditions thermiques des entrepôts frigorifiques car elle permet aux opérateurs d’avoir les mains libres et de ne pas être gênés par les gants.
|
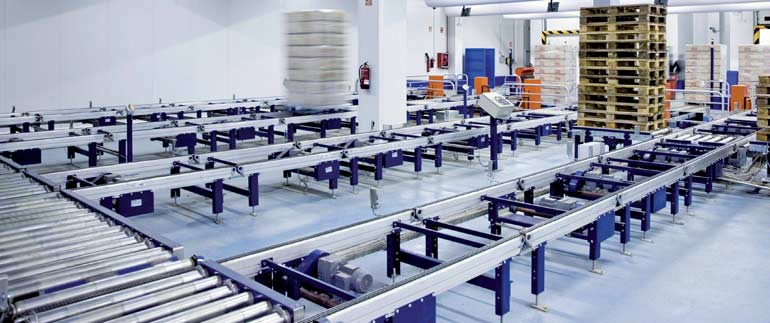
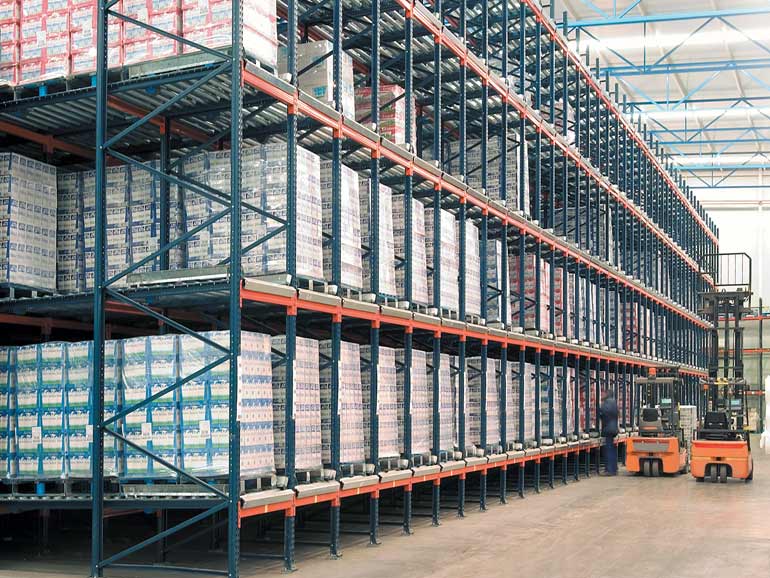
Rayonnages à palettes dynamiques d'une entreprise du secteur alimentaire
Exemple 5. Magasin automatique pour palettes et picking |
|
Dans cette configuration, un magasin automatique pour palettes, desservi par quatre transstockeurs, sert principalement au stockage de la réserve de produits de moyenne et grande consommation, ainsi que la marchandise volumineuse. Face à ce magasin, une plateforme a été installée avec un circuit de convoyeurs et des postes de picking, depuis lesquels la préparation de commande est directement effectuée sur des palettes. L’opérateur dispose de dispositifs d’aide à la préparation, tels que des solutions informatiques et des lecteurs de codes-barres, pour faciliter les opérations de picking et réaliser le réapprovisionnement en marchandises du magasin automatique pour bacs Miniload. Dans les rayonnages à palettes sont stockés les produits à faible consommation, de dimensions moyennes et irrégulières. Des chariots tridirectionnels et préparateurs de commandes à haute élévation sont utilisés pour le réaliser le picking directement sur les rayonnages. Les produits de grande consommation, généralement livrés par palettes complètes, sont stockés sur les rayonnages par accumulation, et leur manutention est réalisée grâce à des chariots à mâts rétractables. Le magasin automatique pour bacs, équipé de neuf transstockeurs, sert au stockage de produits de petite et moyenne taille dans des bacs. Trois circuits de convoyeurs ont également été installés, desservant chacun un niveau du magasin : celui au niveau inférieur transfert les bacs de l’avant du magasin aux postes de préparation de commandes ainsi qu’au circuit de convoyeurs qui dessert la zone de réapprovisionnement. Celui au niveau intermédiaire est utilisé pour les retours et les entrées de bacs dans le magasin, et enfin celui au niveau supérieur envoie les bacs de commandes préparées à la gare de tri. La configuration en trois niveaux évite les interférences et facilite le flux de bacs. Les postes de picking sont ergonomiques pour faciliter la préparation de commandes et éviter les temps morts. Les stockeurs verticaux servent à stocker les composants délicats ou de grande valeur et les produits de petite taille. Au niveau inférieur de la plateforme, des élévateurs établissent la connexion entre le circuit de convoyeurs du niveau inférieur au niveau supérieur, que ce soit pour les palettes ou les bacs. Ils effectuent :
Le circuit aérien de convoyeurs à rouleaux et à bande sur deux niveaux relie les deux magasins automatiques et permet d’acheminer les commandes préparées vers la gare de tri. Celles déjà triées sont consolidées avec celles en provenance des rayonnages à palettes. Les palettes complètes en provenance du magasin automatique pour palettes sont quant à elles directement transférées dans les allées situées devant les quais d’expédition. Pour le transport des palettes dans la zone de réception et d’expédition, les opérateurs utilisent des transpalettes électriques et manuels.
|