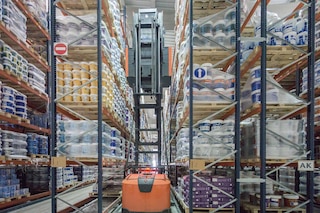
Le sur-stockage : les stratégies pour l'éviter
Le sur-stockage est un des problèmes logistiques les plus courants au sein des installations de stockage. L'excès de stock provient principalement d'une mauvaise planification et/ou coordination entre les différents maillons de la chaîne logistique. Mais, quelles conséquences entraîne-t-il ?
Dans cet article, nous analysons en quoi consiste l'excès de stock, pourquoi il est généré, son impact sur le fonctionnement d'un entrepôt et, surtout, nous présentons trois stratégies visant à supprimer le sur-stockage dans l'entrepôt.
Qu'est-ce que le sur-stockage ?
Le sur-stockage ou excès de stock est l'état dans lequel se trouve l'entrepôt lorsque la matière première et les produits finis stockés au sein de l'installation dépassent largement la demande. Dans ce contexte, les entrées de produits excèdent les sorties et l'entrepôt provoquant un goulot d'étranglement.
Cela est dû à une mauvaise planification et/ou coordination entre les ventes, la logistique et la production, entre autres. Une erreur d'excès de stock due au fait de ne pas attribuer la rotation appropriée à un produit est une erreur couramment commise dans de nombreuses entreprises. De fait, le sur-stockage a généralement lieu dans les installations logistiques approvisionnant ou stockant des produits fabriqués à la chaîne. Mais, pourquoi génère-t-on du sur-stock ?
L'excès de stock peut se produire pour de nombreuses raisons, comme la saisonnalité du produit, la réputation de la marque, l'entrée de nouveaux agents sur le marché et la détérioration des conditions socio-économiques d'un marché.
En ce sens, nous pouvons classer les conditions préalables à un excès de stock en deux grands groupes :
- Les facteurs externes : ils sont le fruit de changements socio-économiques externes à l'activité de l'entreprise. Dans ce cas, l'entrepôt dispose toujours du même stock indiqué dans la planification logistique, mais la demande du produit n'est plus la même. Cela aboutit à une situation dans laquelle l'entrepôt doit réaffecter les ordres d'entrée et de sortie de marchandises pour ainsi rééquilibrer les choses. Un exemple de cela serait un changement de mode ou une crise économique.
- Les facteurs internes : ils proviennent d'erreurs découlant de la propre organisation de l'entreprise. Il peut s'agir d'erreurs logistiques (une mauvaise gestion du stock) ou du service des ventes / achats, qui s'est trompé dans ses prévisions de croissance.
4 problèmes provoqués par l'excès de stock
L'excès de stock dans l'entrepôt peut entraîner d'importants surcoûts logistiques. Voici ses principales conséquences :
- Des flux de mouvements et de marchandises inefficaces : le besoin de stocker plus de marchandises dans l'entrepôt empêche d'établir des itinéraires de dépôt, d'extraction et de picking efficaces au sein de l'installation. Plus le volume d'articles à stocker sera important, plus il sera difficile d’organiser la marchandise dans l'entrepôt.
- La détérioration du stock : une négligence au niveau du contrôle des entrées et des sorties peut mettre en péril la traçabilité des produits. Il faut faire particulièrement attention à ce point dans des secteurs comme l'industrie pharmaceutique ou l'industrie alimentaire, dont les produits sont régulés au moyen d'une date de péremption ou d'une date limite de consommation. Si le stock de chaque référence dans l'entrepôt est trop élevé, le risque de commettre des erreurs lors d'opérations comme la préparation de commandes ou l'expédition d'articles est plus important.
- La hausse du coût de stockage : un excès de stock entraîne un investissement plus important dans le sol logistique et des dépenses supplémentaires en équipements et en ressources humaines pour gérer l'entrepôt.
- La mauvaise réputation de l'entreprise : toute erreur commise dans n’importe quelle opération de l'entrepôt va à l'encontre d'un service logistique de qualité. En cas d'excès de marchandises, il est donc plus probable que les opérateurs commettent des erreurs dans les bons de commande, provoquant l'insatisfaction et potentiellement des plaintes de la part du client final. De nos jours, cela constitue un risque majeur , particulièrement crucial en raison de l'essor du e-commerce. Une mauvaise expérience utilisateur peut conduire les clients à se tourner vers la concurrence.
L'excès de stock entraîne la réduction des marges bénéficiaires de l'entreprise, soit en raison d'une baisse de la demande, soit parce que, suite à un accroissement de l'offre, l'entreprise doit réinvestir dans des installations de stockage pour augmenter leur capacité. Bien souvent, la solution ne passe pas par l'acquisition de mètres logistiques supplémentaires, mais par la mise en œuvre de systèmes de stockage classiques ou automatisés adaptés au flux de travail de l'installation.
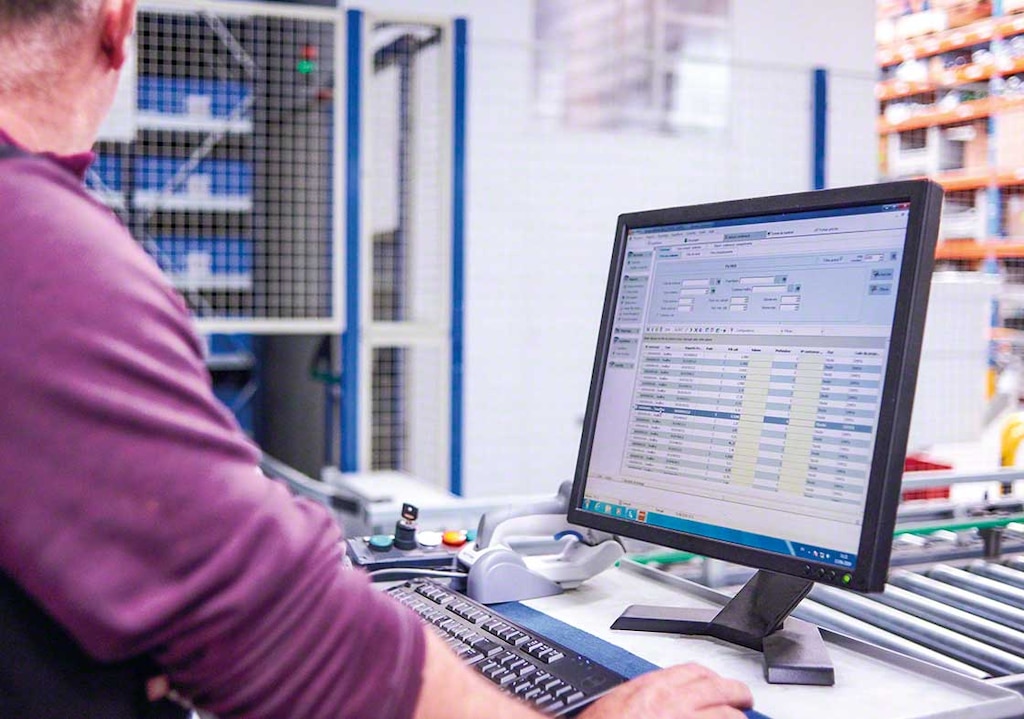
3 stratégies pour remédier au sur-stockage
L'excès de stock est un problème pouvant être endigué au moyen de solutions intralogistiques garantissant l'efficacité et la productivité de l'entrepôt. Bien que chaque entreprise ait des besoins spécifiques, voici les trois stratégies principales pour réduire le sur-stockage :
- Le système de gestion d'entrepôt (WMS) : un outil numérique comme un système de gestion d'entrepôt prévoit l'offre précise de stock à partir de la demande de chaque UGS et de ses caractéristiques. Le logiciel optimise donc le flux de travail de l'entreprise, évite l'excès de stock de chaque référence et attribue les emplacements de produit et les itinéraires de picking les plus appropriés. Tout cela dans le but de maximiser la productivité de l'installation.
- Les systèmes de stockage appropriés : qu'elles soient classiques ou automatisées, l'installation doit miser sur des solutions s'adaptant aux besoins réels de l'entreprise. Par exemple, lorsque la rotation des produits ne constitue pas une priorité, les rayonnages par accumulation exploitent au maximum la capacité de stockage, ce qui évite d'avoir un excès de stock pour certains produits.
- Des méthodes de travail optimisées : il est possible de réduire le sur-stockage au moyen d'opérations comme la production just-in-time ou la stratégie logistique de cross-docking. Dans les deux cas, l'entrepôt ne requiert pas un grand nombre de références, puisqu'il se coordonne avec d'autres installations pour disposer de la matière première ou du produit semi-fini au moment opportun.
Le sur-stockage : un fardeau pour l'entrepôt
La multiplication des canaux de vente, autrement dit l'omnicanalité, a modifié la relation entre le client et l’entreprise. Actuellement, les organisations doivent maximiser leur efficacité pour rester compétitives dans un contexte de plus en plus complexe.
C'est pour cette raison que la manière d'optimiser les ressources de l'entrepôt, notamment pour réduire les coûts, est une des premières stratégies logistiques que toute entreprise doit déterminer. Dans ce contexte d'entrepôts de plus en plus hétérogènes, les entreprises doivent miser sur de nouvelles méthodologies leur permettant d'être efficaces, même lorsqu'elles n'ont pas toutes leurs UGS en stock.
Une bonne gestion des commandes en cours (backordering) part de la simplification des processus logistiques et de la mise en œuvre de systèmes de stockage automatisés et d'outils numériques, assurant une productivité optimale et l'élimination d'erreurs au sein de l'installation.
Chez Mecalux, nous offrons depuis plus de 50 ans des solutions intralogistiques garantissant la productivité au sein de chaque installation. Si votre entrepôt est en situation de sur-stockage, n'hésitez pas à nous contacter. Un expert sera ravi de vous proposer la meilleure solution pour votre activité.