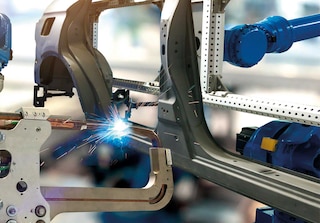
Le MRP : un jalon important dans le processus de production
Le management des ressources de production constitue un défi logistique complexe pour toute installation. Quelle est la quantité de matières premières dont j'ai besoin, quand en ai-je besoin ou quel nombre d'unités doivent être produites, sont certaines des questions auxquelles les fabricants répondent, depuis des décennies, au moyen du système MRP (Material Requirements Planning).
Dans cet article, nous analyserons tout ce qui entoure le management des ressources de production : sa définition, son fonctionnement, ses avantages et pourquoi cela a été et est aussi important au sein du processus de production. De plus, nous expliquerons la différence entre un système MRP et un ERP.
Qu'est-ce qu'un MRP ?Le management des ressources de production ou Material Requirements Planning est un système conçu pour gérer les processus de production et coordonner au préalable les activités de fabrication, d'achat et de livraison du produit fini.
Le système MRP a fait son apparition dans les années 1970 et a connu une croissance fulgurante. Il est tiré du livre Production Planning and Control: A Comprehensive Approach, écrit par D.R. Kiran en 1975, on estime que déjà 700 entreprises utilisaient le système MRP pour optimiser leurs processus de production. Ce chiffre a augmenté de 174 % par an, jusqu'à arriver à 8 000 entreprises en 1981, en six ans seulement.
Aujourd'hui, le système MRP est considéré comme l'origine des programmes informatiques actuels visant à améliorer les processus industriels : MRP II (Manufacturing Resource Planning), ERP (Enterprise Resource Planning), CRM (Customer Relationship Management), SRM (Supplier Relationship Management) ou MES (Manufacturing Execution System).
Le MRP organise les activités de fabrication et optimise la gestion du stock en fonction des besoins des entreprises. Le Material Requirements Planning permet à n'importe quel fabricant de se rapprocher de son principal objectif : disposer à tout moment de la quantité de ressources exacte pour produire les produits et les livrer aux clients dans les plus brefs délais et au moindre coût possible.
Comment est-ce qu'un MRP fonctionne ?
Le système MRP a besoin de données d'entrée qui sont indispensables :
- Le plan directeur de production : connu comme le MPS (Master Production Schedule), il indique le nombre d'articles qui seront produits et sur quels laps de temps.
- La nomenclature : le BOM (bill of materials) indique les matières premières, leur quantité et les processus de production nécessaires afin d'obtenir une unité de produit fini.
- Le livre d'inventaire : il détaille les informations liées au stock (inventaire disponible, stock sous commande, commandes annulées, temps d'attente, etc.). L'objectif est de savoir quelle matière première est disponible afin de pouvoir l'utiliser immédiatement.
Avec toutes ces données d'entrée en main, le système de management des ressources de production offre les données de sortie suivantes :
- Le plan directeur de production recommandé : il établit un calendrier comprenant les dates liées au processus de production (début et fin), les quantités pour chaque étape de la feuille de route et la nomenclature (BOM). Tout cela vise à répondre à la demande indiquée dans le plan directeur de production.
- Le programme d'achats recommandé : il indique les dates auxquelles le matériel acheté sera reçu, ainsi que les dates auxquelles il faudra commencer à préparer les nouvelles commandes pour qu'elles coïncident avec le plan directeur de production.
Le système MRP permet donc de recevoir le matériel approprié afin de maintenir un niveau de stock minimal pour approvisionner le site de production, tout en garantissant une planification efficace des activités de fabrication, d'achat et de livraison du matériel.
Exemple de management des ressources de production
Après avoir dressé le plan directeur de production et la nomenclature, il est établi que, pour fabriquer un produit fini (produit X), il faut 2 unités du matériel A et 1 unité du matériel B. Pour chaque unité du matériel A, il faut 3 unités de la pièce C et, pour chaque unité de matériel B, il faut 2 unités de la pièce C et 4 unités de la pièce D.
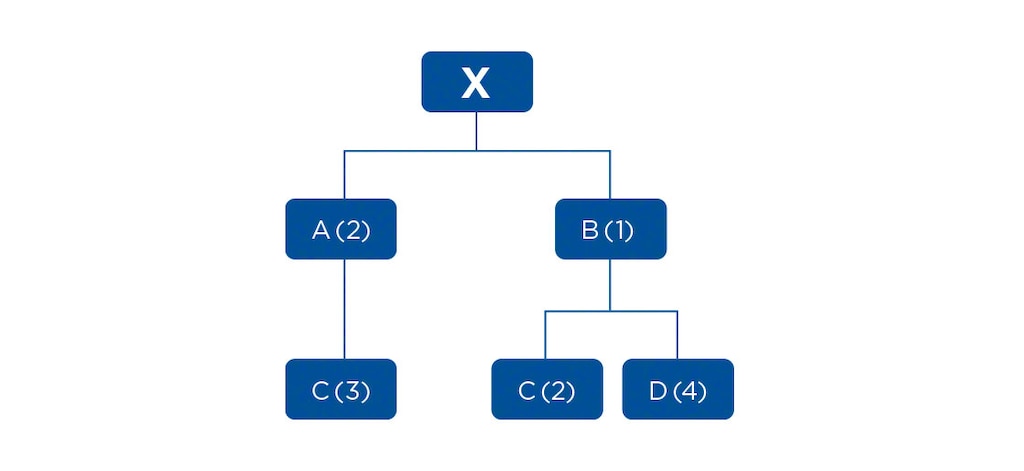
Ci-après, nous décrivons en détail le livre d'inventaire (IRF, Inventory Record File), qui reflète le stock disponible et le temps d'attente (lead time) pour recevoir chaque produit :
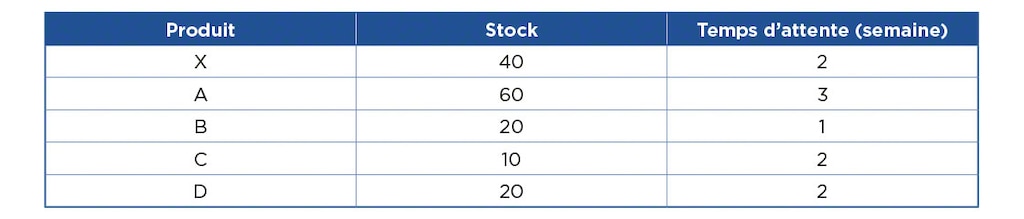
Voici le résumé du management des ressources de production pour la fabrication de 100 unités du produit X en 10 semaines :
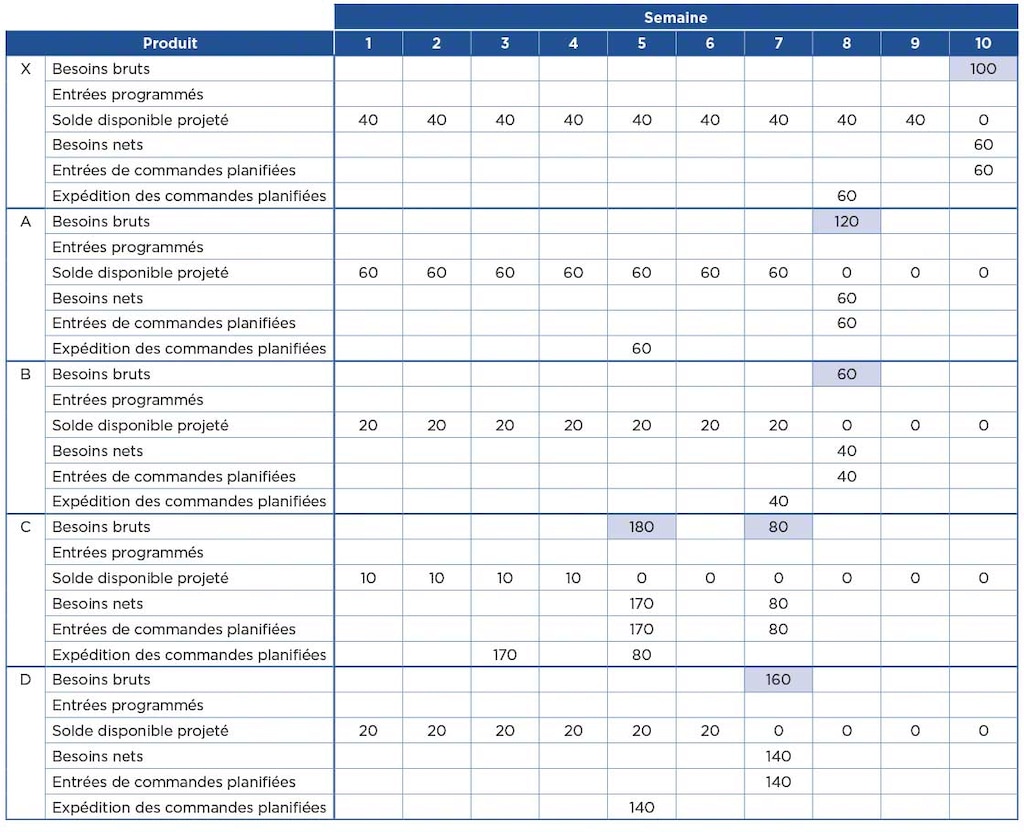
Il en ressort que, pour disposer de 100 unités du produit X en semaine 10, il faut 60 unités supplémentaires, qui s'ajouteraient aux 40 unités déjà disponibles dans l'inventaire. Étant donné que, dans le livre d'inventaire, nous avons défini que le temps d'attente (lead time) pour le produit X est de 2 semaines, la commande devra être passée en semaine 8.
Si chaque unité du produit X requiert 2 unités du produit A, 120 unités du produit A seront donc nécessaires en semaine 8. Comme l'inventaire dispose déjà de 60 unités, le besoin net du produit A sera aussi de 60 unités. Compte tenu du temps d'attente, il faudra demander les unités en question trois semaines à l'avance.
Les besoins nets des produits B, C, D et F sont établis selon la même procédure, tout comme la semaine à laquelle les demander.
Les fonctions d'un MRP et les avantages de son utilisation
Au sein d'un processus de production, le management des ressources de production a pour fonction de calculer la quantité de matière première nécessaire, les composants requis et la quantité de produit fini qui sera fabriquée.
Le management des ressources de production offre les avantages suivants :
- L'entière disponibilité de la matière première pour la production.
- Le respect des délais de livraison.
- Le maintien d'un faible niveau de stock, aussi bien de matière première que de produit fini.
- La planification des activités de fabrication, des bons de livraisons et des ordres d'achats.
- La réduction des coûts.
Le système MRP résout les problèmes auxquels les fabricants sont confrontés chaque jour, notamment en termes d'achat de matière première. Un achat incorrect ou insuffisant peut prolonger les délais de livraison et l'achat de matériel superflu entraîne un surcoût de stockage.
Les différences entre MRP et MRP2
Au début des années 1980, le système MRP (Material Requirements Planning) a évolué vers le MRP2 (Manufacturing Resource Planning), un système de planification avancé à plus large portée. D’une manière générale, les principales différences entre les deux systèmes sont les suivantes :
- En plus de planifier la gestion des ressources requises pour la production, le MRP2 intègre d'autres services de l'entreprise, comme le département commercial, financier, etc.
- Tandis que le MRP travaille en fonction du plan directeur de production, le MRP2 se fonde sur l'étude de la demande et du marché.
- Le MRP2 analyse le comportement de l'entreprise pour exécuter une planification efficace, tandis que le MRP le fait par le biais de la pratique et de l'expérience préalable de l'entreprise.
- Le MRP est un système ouvert, contrairement au MRP2, qui est clos. Cela veut dire que le MRP2 est capable de prendre en compte les rapports qu'il dresse, et ainsi effectuer des replanifications davantage adaptées à la réalité.
Le MRP2 est la version modernisée du MRP. En plus de répondre aux questions de la quantité à produire et à quel moment, il définit aussi les ressources, la quantité et le moment appropriés pour réaliser ladite production.
Les différences entre MRP et ERP
Le système ERP (Enterprise Resource Planning) a été utilisé pour la première fois dans les années 1990 et il est encore plus complet et polyvalent que ses prédécesseurs. L'élément qui le caractérise et le différencie des MRP est le fait qu'il est capable de centraliser toutes les tâches de l'entreprise en un seul et même système.
Autrement dit, le MRP est un logiciel qui fonctionne seul, tandis que l'ERP intègre et combine les systèmes informatiques utilisés par chaque service afin de créer une base de données centralisée. N'importe quel service de l'entreprise peut ainsi accéder aux informations en temps réel, contrôler les flux de travail, minimiser les erreurs et communiquer avec d'autres services.
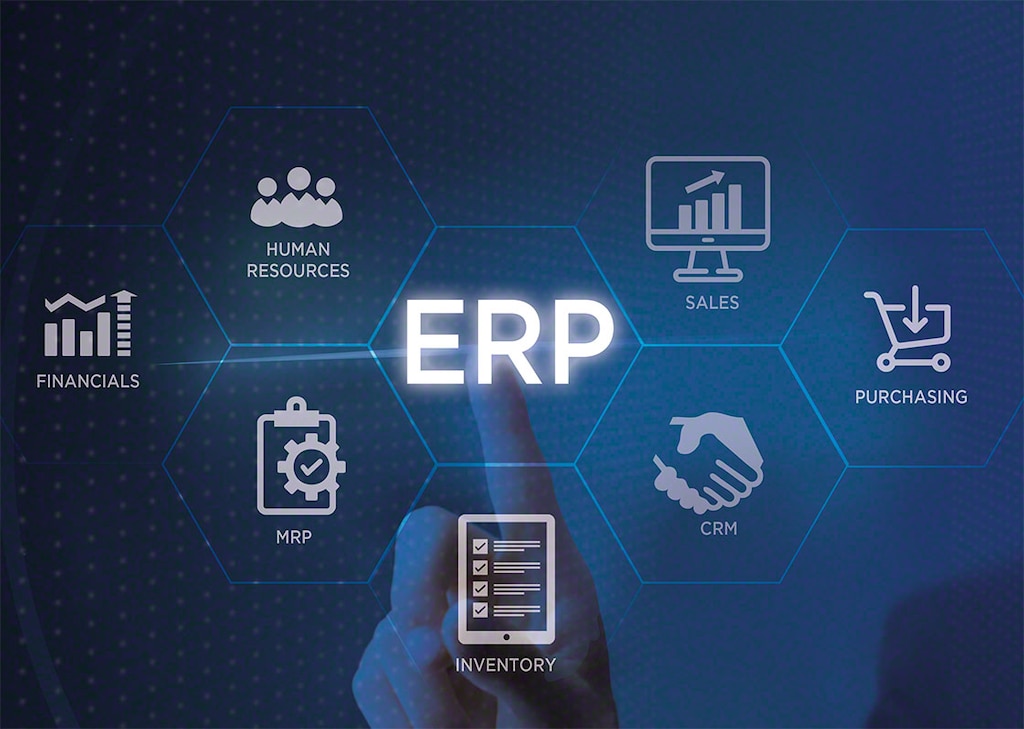
Le MRP : dans le sillage des progrès technologiques
Après cinquante ans de fonctionnement, il est juste de conclure que le management des ressources de production a marqué un tournant dans le processus de production. Son principe, qui n'est autre que l’anticipation des besoins en vue de la planification, s'est adapté aux nouvelles technologies afin d’améliorer la rentabilité de la chaîne logistique.
Chez Mecalux, nous misons constamment sur les solutions technologiques les plus novatrices du marché, tant en termes de stockage que de gestion logistique, comme c'est le cas avec Easy WMS. Ce système peut être intégré avec n'importe quel ERP, de sorte que les deux systèmes échangent des données et des informations visant à obtenir une plus grande productivité dans l'entrepôt.
Contactez-nous, nos spécialistes vous conseilleront et vous aideront à tirer le meilleur parti de votre chaîne logistique.